Additive manufacturing technology is an advanced manufacturing technique that integrates mechanics, computing, CNC, and materials. It enables the rapid production of intricate components. Originating in the 1980s, its fundamental principle simplifies three-dimensional processing into two-dimensional layers, accumulating point by point or layer by layer to ultimately obtain solid components or prototypes. Compared to traditional manufacturing methods, additive manufacturing technology offers advantages such as high design flexibility, short product development cycles, and low manufacturing costs.
Additive manufacturing techniques for ceramic components can be classified into four categories based on the form of raw materials: powder-based, filament-based, sheet-based, and liquid-based. Each technology has its characteristics and applications. For instance, Three-Dimensional Printing (3DP) employs binder jetting to solidify powder, suitable for manufacturing porous ceramic components, primarily applied in the field of biomedical tissue engineering. Laser Selective Sintering (SLS) utilizes laser scanning on powder without the need for support structures, ideal for producing intricately shaped components, albeit with higher costs.Is there anything else you would like me to translate or improve for you?
Other techniques such as laser selective melting, fused deposition modeling, layered solid manufacturing, and photo-curing molding are also introduced, with each technology having its principles, characteristics, and application scope. Among them, photo-curing molding technology includes SLA and DLP, offering high manufacturing precision and surface quality. However, it also faces challenges such as high material costs, environmental pollution, and equipment expenses.
In general, additive manufacturing technology holds vast prospects in the manufacturing of ceramic components, meeting the demands for the production of intricate structural parts.Is there anything else you would like me to translate or improve for you?
1、三维打印
1)3DP 技术的原理
2)3DP 技术的特点
3)3DP 技术的应用
4)3DP陶瓷致密化
2、激光选区烧结
1)SLS技术的原理
2)SLS技术的特点
(1)与 3DP 类似,SLS 受粉末性质的影响,成型件的精度及表面粗糙度较差且 SLS 不适合制造具有细小微观孔(<500µm)的陶瓷零件;
3、激光选区熔化
1)SLM技术的原理
2)SLM技术的特点
4、熔融沉积造型
1)FDM技术的原理
2)FDM技术的特点
(1)原材料制备成卷轴丝的形式,易于搬运及更换;
5、分层实体制造
1)LOM技术的原理
2)LOM技术的特点
(1)成型效率高,利用激光直接对片材进行切割,显著提高了成型效率;
(2)无需支撑结构就能制造复杂形状零件,因此前期处理工作量较小;
(3)制造成本低;
(4)不受设备工作台限制,可以制造较大尺寸工件;
(1)制造的零件质量受层与层之间粘结效果的影响,常常存在分层,交界面出现孔隙及各个方向机械性能不一致等问题。
6、光固化成型
1)SLA技术的原理
2)SLA技术的特点
(1)光敏树脂价格昂贵且一般具有毒性,容易造成环境污染;
(2)激光器的价格及使用寿命有限导致制件的成本较高;
3)SLA技术的应用
7、光固化面成型
1)DLP的原理
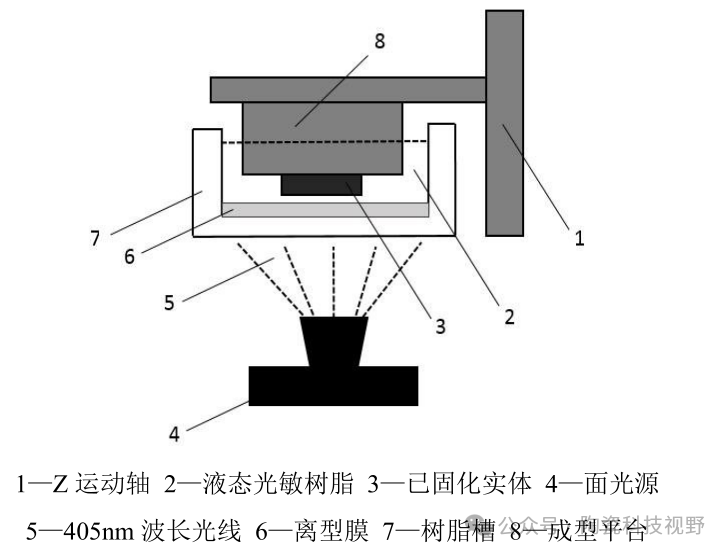
2)DLP 技术的特点
(1)超快速的光线切换和整体投影使DLP 3D打印处理时间比传统的SL点-线-面扫描过程明显缩短,而且可以获得微米级的特征分辨率,从而能够更快速和更高精度地制造零件;
3)DLP 技术的应用
陶瓷光固化3D打印技术研究进展,刘雨 , 陈张伟.
电子雾化与HNB产品都是新型电子产品,结构虽小,却融合应用多种材料、表面处理、芯片电子等技术工艺,而且雾化技术一直在不断更迭,供应链在逐步完善,为了促进供应链企业间有一个良好的对接交流,艾邦搭建产业微信群交流平台,欢迎加入;Vape e-cigarettes (VAPE) and Heat-Not-Burn e-cigarettes (HNB) are both emerging electronic products. Despite their compact size, they integrate various materials, surface treatment technologies, chip electronics, and other advanced technical processes. Moreover, atomization technology is constantly evolving and the supply chain is being progressively perfected. To facilitate good communication and networking among supply chain enterprises, Aibang has established an industry WeChat group communication platform and warmly welcomes interested enterprises to join.
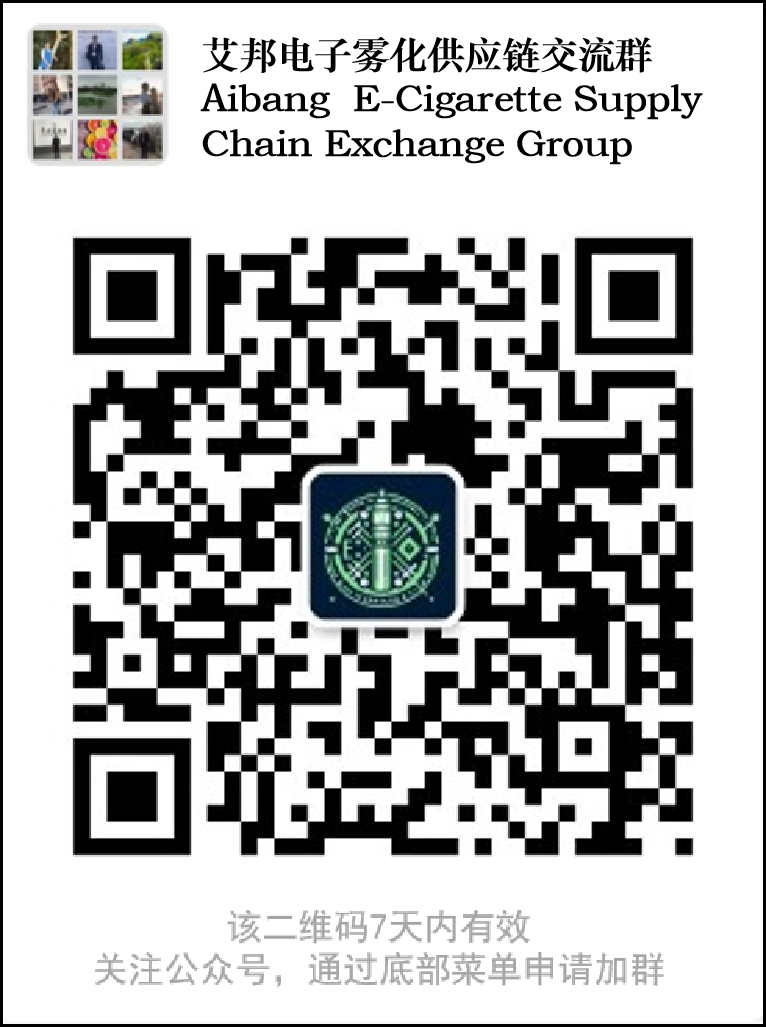